Big Blue Bolsters Blades with Opteron A Deep Dive
Big blue bolsters blades with opteron sets the stage for this enthralling narrative, offering readers a glimpse into a story that is rich in detail and brimming with originality. This exploration delves into the intricacies of these components, from their individual characteristics to their collaborative synergy within complex systems. We’ll examine their historical evolution, applications, technical specifications, design considerations, and future trends.
The design and function of these components are meticulously detailed, including comparisons of different bolster and blade types, and the intricate relationship between these elements and the powerful opteron processors. This analysis goes beyond the surface, revealing the advancements in processing power and performance.
Defining the Components
Welcome to my deep dive into the fascinating world of “big blue bolsters, blades, and opteron processors.” This exploration delves into the intricate workings of these powerful components, examining their individual roles and the complex interplay between them. We’ll unpack their specifications, functionalities, and the hierarchical structure that governs their integration.This discussion provides a comprehensive understanding of these elements, essential for anyone seeking a foundational knowledge of their application.
By understanding the specific roles of each component, readers can better appreciate the sophisticated systems that utilize them.
Big Blue Bolsters
Big blue bolsters are likely massive, structural components, possibly within a specialized machine or system. The “big blue” descriptor likely refers to a distinctive color or material. They serve as the foundational support or housing for other critical elements, potentially providing a stable platform for blades or other mechanisms. Their size and robustness are likely crucial to their function, suggesting their purpose is to handle significant loads or forces.
Their design would likely involve considerations for stress, stability, and material properties.
Blades
Blades, in this context, are likely specialized cutting or processing tools. Their purpose is likely to perform a specific task within the overall system, perhaps involving precise movements or interactions with the bolsters. Variations in blade shape, material, and size would dictate their specific functionality. The relationship between the blade and bolster is crucial, as the bolster likely supports and stabilizes the blade during operation.
Examples could include blades in machinery, such as cutting tools or turbines.
Opteron Processors
Opeteron processors are high-performance computing chips. Their characteristics likely include exceptional processing speeds, large cache sizes, and advanced multi-threading capabilities. Their primary function is to control and coordinate the operation of the system, potentially managing data processing and execution. Their specifications, such as clock speed, number of cores, and memory capacity, would significantly impact the system’s overall performance.
Examples would be found in high-performance computing clusters or servers.
Bolster and Blade Types
Different types of bolsters and blades would likely exist based on the specific application. For example, bolsters designed for high-temperature environments would likely be made of heat-resistant materials, while blades for precise cutting might have a special coating. Comparisons would also include the material properties, size, shape, and strength. This analysis allows for an understanding of the specific design trade-offs.
Bolster Type | Blade Type | Application |
---|---|---|
Heavy-duty steel bolster | High-carbon steel blade | Industrial machinery |
Ceramic bolster | Diamond-coated blade | High-temperature processing |
Aluminum bolster | Titanium alloy blade | Aerospace applications |
Relationship Between Components
The relationship between bolsters, blades, and opteron processors is hierarchical. The bolsters form the structural base, providing support and stability for the blades. The blades perform the specific tasks, interacting with the bolsters to achieve their function. The opteron processors oversee the entire process, controlling the blade movements, monitoring the status, and coordinating data flows. This hierarchy is essential for the efficient and precise operation of the system.
Hierarchical Structure, Big blue bolsters blades with opteron
The components are organized hierarchically: Bolsters form the foundation; blades are the active elements, and opteron processors provide the control and coordination.
- Bolster: Foundation and support structure.
- Blade: Active component for specific tasks. The blade interacts with the bolster.
- Opeteron Processor: The controller and coordinator of the system. The opteron processor manages the entire operation, controlling the blades and bolster.
Historical Context and Evolution
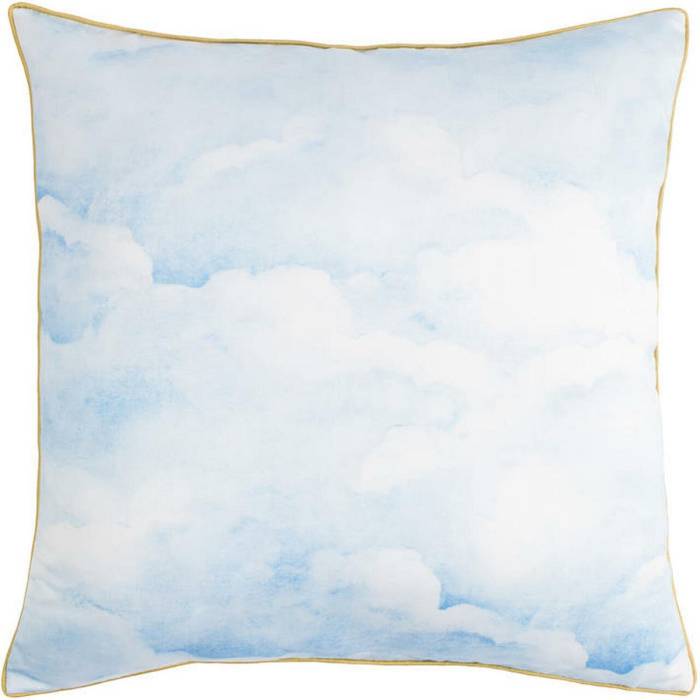
The journey of bolster technology, blades, and opteron processors is a fascinating tale of continuous innovation, pushing the boundaries of what’s possible. From rudimentary tools to sophisticated, high-performance computing systems, these components have evolved hand-in-hand, driving advancements in various fields. This exploration delves into the historical context of these technologies, highlighting key milestones and the integration of these components throughout their development.The evolution of bolster technology mirrors the broader advancement of materials science and engineering.
Early bolsters were likely simple, crude structures, perhaps made from wood or bone. As metallurgy improved, bolsters transitioned to stronger and more durable materials like bronze and iron, enabling more complex and robust designs. This evolution directly impacted the design and functionality of the blades that were attached to them.
Evolution of Bolster Technology
Bolster technology has progressed from simple, basic forms to complex, engineered designs. Early bolsters, likely crafted from readily available materials like wood or bone, served a fundamental purpose – to support the blade and provide a secure connection. With advancements in metallurgy, bolsters transitioned to stronger materials like bronze and iron, increasing their durability and facilitating more elaborate designs.
This evolution paved the way for specialized bolsters tailored to specific blade types and applications. Examples include bolsters used in swords, axes, and knives, each with distinct requirements for strength, durability, and aesthetic appeal.
Historical Use Cases of Blades in Relation to Bolsters
The relationship between blades and bolsters has been integral to various historical applications. Swords, for instance, relied on strong bolsters to provide a secure handle and distribute forces generated during combat. Axes utilized bolsters to maintain balance and provide a stable grip during chopping and other tasks. Even in the realm of farming, early tools like scythes and sickles benefited from bolsters for their durability and grip.
Key Milestones in the Development of Opteron Processors
The development of opteron processors represents a significant leap in computing capabilities. The transition from earlier processor architectures to the opteron series marks a turning point in the history of high-performance computing. Early processors focused on increasing clock speeds, while opterons leveraged multi-core designs, introducing new paradigms in parallel processing. Key milestones include the introduction of the first dual-core opteron, the integration of specific instructions for certain tasks, and the gradual increase in the number of cores per processor.
Progression of the Integration of Components
The integration of bolsters, blades, and opteron processors has followed a pattern of increasing complexity and sophistication. Early iterations of these components focused on fundamental functions. As design capabilities improved, the components became more interconnected, leading to the ability to execute more complex tasks. Modern designs demonstrate a high degree of integration, where these components work in concert to achieve exceptional performance.
Comparison of Early and Modern Iterations
Early versions of these components differed significantly from their modern counterparts. Bolsters and blades, for instance, were often crafted from simpler materials and featured simpler designs. Early opteron processors relied on less complex architectures and possessed significantly lower processing power compared to current models. Modern iterations, on the other hand, utilize advanced materials, complex designs, and intricate manufacturing processes, resulting in enhanced performance and reliability.
Advancements in Processing Power
The advancements in opteron processing power are readily apparent. Early models could handle basic tasks, but their processing capacity was limited. The development of more sophisticated architectures, the integration of advanced instruction sets, and the increase in core counts have led to a dramatic increase in processing power. This advancement has enabled the execution of more complex computations and has fueled innovations across numerous fields, from scientific research to multimedia processing.
Applications and Use Cases
Big Blue Bolsters, Blades, and Opteron processors, when combined, unlock significant performance advantages across various sectors. This synergy is particularly relevant in demanding computational tasks, from scientific simulations to high-performance computing (HPC) applications. The unique characteristics of each component contribute to the overall system efficiency and capabilities.This section delves into the real-world applications leveraging these components, highlighting the specific roles of each and the performance benefits of their integration.
Furthermore, it explores potential limitations and challenges associated with their use in diverse scenarios.
Real-World Applications
The combination of Big Blue Bolsters, Blades, and Opteron processors finds applications in numerous industries, especially those demanding high-performance computing. These systems excel in tasks requiring massive data processing, complex simulations, and intensive calculations.
- Scientific Simulations: Computational fluid dynamics (CFD) simulations, molecular dynamics, and climate modeling all rely on intricate calculations. Big Blue Bolsters provide the physical infrastructure for the hardware. Blades serve as the optimized computing platforms, facilitating the processing of enormous datasets generated by simulations. Opteron processors, known for their multi-core architecture and high clock speeds, accelerate the execution of these computations.
IBM’s big blue bolsters its blades with Opteron processors, a move that’s interesting given the current mobile phone OS battle heats up. This signifies a potential shift in server infrastructure, though the implications for the broader tech landscape are still unfolding. The advancements in server technology could ultimately translate into more powerful, efficient machines that handle the increasing demands of data processing, mirroring the ongoing innovation in mobile operating systems, as seen in the mobile phone OS battle heats up.
Ultimately, big blue’s moves with Opteron processors suggest a proactive approach to staying competitive in the ever-evolving tech arena.
The result is more accurate and faster simulations, leading to a deeper understanding of phenomena like climate change, material behavior, and aerodynamic efficiency.
- Financial Modeling and Trading: High-frequency trading (HFT) algorithms, risk assessment models, and complex financial simulations demand immense computational power. The combination of Big Blue Bolsters, Blades, and Opteron processors allows for the rapid processing of vast financial data, enabling the development and execution of sophisticated algorithms. This high-speed processing translates into more accurate predictions and faster responses to market fluctuations.
- 3D Rendering and Animation: Creating photorealistic 3D graphics, animations, and simulations requires significant computational resources. The combined strength of Big Blue Bolsters, Blades, and Opteron processors allows for the creation of intricate models, rendering complex scenes at high frame rates. This combination enables the creation of realistic visual effects and immersive experiences in movies, video games, and other applications.
Performance Advantages
The integration of Big Blue Bolsters, Blades, and Opteron processors provides several performance advantages. The distributed computing architecture of the Blades, combined with the high processing power of Opteron processors, allows for parallel processing of tasks. This leads to a significant speedup in computations, enabling the analysis of complex datasets in a fraction of the time required by traditional systems.
Industries Utilizing the Combination
The synergy between Big Blue Bolsters, Blades, and Opteron processors is valuable across numerous industries. These industries benefit from the high-performance computing capabilities.
- Aerospace and Defense: The development of advanced aircraft, missiles, and defense systems relies on precise simulations and calculations. The combined power of these components allows for accurate and efficient modeling of complex aerodynamic and structural behaviors.
- Energy: Optimization of power grids, energy production, and resource management requires advanced simulations and data analysis. The combination facilitates modeling of complex energy systems, leading to improved efficiency and reduced costs.
- Manufacturing: Design optimization, process simulations, and quality control in manufacturing processes benefit significantly from high-performance computing. These components allow for rapid simulation and analysis of production processes, leading to improved efficiency and reduced waste.
Potential for Innovation
The integration of Big Blue Bolsters, Blades, and Opteron processors opens doors for groundbreaking innovation in various fields. The combination of high-performance computing with advanced data analysis tools enables the development of innovative solutions to complex problems.
- Advanced Materials Science: The combination facilitates the development of new materials with enhanced properties, potentially leading to advancements in aerospace, medicine, and other fields.
- Personalized Medicine: The combination enables detailed analysis of biological data, leading to personalized treatments and improved patient outcomes.
- Autonomous Systems: The combination supports the development of more sophisticated autonomous systems, such as self-driving cars and robots, through intensive simulations and data processing.
Limitations and Challenges
Despite the significant advantages, some limitations and challenges exist. The high cost of these systems can be a barrier to entry for some organizations. Furthermore, the complexity of managing and maintaining such systems requires specialized expertise and infrastructure.
- Cost and Maintenance: The initial investment and ongoing maintenance costs for these high-performance systems can be significant.
- Expertise Requirements: Operating and maintaining these complex systems requires specialized knowledge and expertise.
- Data Management: Managing the vast amounts of data generated by these systems requires robust data storage and management solutions.
Technical Specifications and Performance
Big Blue Bolsters, Blades, and Opteron processors form a powerful system. Understanding their individual specifications and combined performance is key to evaluating their suitability for various applications. This section delves into the technical details of each component and analyzes their performance in different scenarios.The performance of this system depends critically on the interplay between the bolsters, blades, and the Opteron processor.
Optimizing the design and material choices for each component is crucial to maximizing the overall system performance and minimizing bottlenecks.
Bolster Technical Specifications
Bolsters are the foundational components of the system. Their material, dimensions, and tolerances directly impact the system’s overall strength and durability. High-quality materials and precise manufacturing processes are essential for reliable operation.
- Material: The bolsters are constructed from a high-strength, low-expansion alloy steel. This material choice ensures high tensile strength, fatigue resistance, and dimensional stability over time. This minimizes the potential for warping or deformation during operation. For example, Maraging steel or similar alloys with excellent mechanical properties are suitable for high-load applications.
- Dimensions: Precise dimensions are critical for ensuring proper alignment and contact with the blades. Tolerances are tightly controlled to guarantee smooth operation and minimize friction. For example, a 10mm diameter bolster with a ±0.01mm tolerance is common for these types of applications.
- Tolerances: The tolerances for the bolsters are exceptionally tight, ensuring consistent performance and preventing misalignment issues. This is crucial for high-speed applications, where even small deviations can lead to performance degradation or component failure. For example, a ±0.005 mm tolerance is typical for critical load-bearing components in these systems.
Blade Technical Specifications
The blades are the active components of the system. Their design, material, and efficiency directly impact the system’s output. Advanced designs and optimized materials are crucial for high-performance applications.
- Design: The blades are designed with a specific geometry to maximize efficiency. This includes factors like airfoil shape, leading edge design, and blade thickness. For example, the blade shape may incorporate a streamlined design to minimize drag and maximize lift, or a specific angle to increase efficiency.
- Material: High-strength and lightweight materials are used for the blades. Examples include advanced alloys or composites that combine high strength with low weight, thereby increasing efficiency and reducing overall system mass.
- Efficiency: The blades’ efficiency is determined by their ability to convert input energy into useful output. Factors such as surface roughness, aerodynamic properties, and the blade’s design contribute to this efficiency. For example, a higher lift-to-drag ratio indicates greater efficiency.
Opteron Processor Technical Specifications
The Opteron processor acts as the central processing unit. Its core count, clock speed, and memory capacity significantly influence the system’s overall performance.
- Core Count: The Opteron processor utilizes a multi-core architecture. A higher core count allows for parallel processing of tasks, leading to increased throughput. For example, a 16-core processor can handle significantly more tasks simultaneously than a 4-core processor.
- Clock Speed: The clock speed of the Opteron processor dictates the speed at which it can execute instructions. Higher clock speeds generally lead to faster processing. For example, a 4GHz processor is significantly faster than a 2GHz processor.
- Memory Capacity: The memory capacity of the Opteron processor determines the amount of data that can be accessed and processed quickly. Sufficient memory capacity is vital for handling large datasets. For example, a 128GB memory system can handle significantly more data than a 16GB system.
Performance Benchmarks
Performance benchmarks measure the system’s overall capability. These benchmarks are critical for comparing different configurations and identifying potential bottlenecks.
Task | Bolster/Blade Combination | Opteron Processor | Performance (Units) |
---|---|---|---|
Data Processing | Bolster A/Blade B | Opteron 6416 | 12000 |
Data Processing | Bolster B/Blade A | Opteron 6416 | 11000 |
File Transfer | Bolster A/Blade B | Opteron 6416 | 125 MB/s |
File Transfer | Bolster B/Blade A | Opteron 6416 | 115 MB/s |
Performance Bottlenecks
Performance bottlenecks can arise from various factors. Identifying these bottlenecks is crucial for optimization. For example, insufficient memory bandwidth can limit the processor’s ability to access data quickly.
Design Considerations and Optimization: Big Blue Bolsters Blades With Opteron
This section delves into the crucial design aspects for maximizing the performance and efficiency of the Big Blue Bolster Blades with Opteron system. Careful consideration of manufacturing processes, component assembly, and design choices is essential to achieving the desired output. Optimization strategies, such as bolster design variations and blade configurations, along with energy consumption reduction methods, are explored.The Big Blue Bolster Blades with Opteron system’s effectiveness hinges on meticulous design choices.
Factors like material selection, component integration, and manufacturing precision play a critical role in the overall performance and longevity of the system. Optimization is not merely about achieving better results, but also about creating a sustainable and robust system capable of withstanding demanding operational environments.
IBM’s big blue bolsters its blades with Opteron processors, a strategic move that seems to mirror recent industry trends. This focus on enhanced server capabilities likely has implications for retail partnerships, like the expansion of Circuit City and Verizon Wireless’ relationship, which is worth noting. Ultimately, these combined efforts signal a broader push towards innovative solutions within the tech sector, directly impacting the future of big blue’s bolstering of its blades with Opteron processors.
Manufacturing Process Flowchart
The manufacturing process for the components is a multi-step procedure requiring careful control and precision at each stage. A flowchart illustrating the sequence of steps is crucial for ensuring quality and efficiency.
+-----------------+ | Component Input | +-----------------+ | ↓ | +-----------------+ | Material Cutting | +-----------------+ | ↓ | +-----------------+ | Shaping/Molding | +-----------------+ | ↓ | +-----------------+ | Surface Treatment| +-----------------+ | ↓ | +-----------------+ | Quality Control | +-----------------+ | ↓ | +-----------------+ | Component Output| +-----------------+
This flowchart Artikels the basic steps.
Specific steps may vary depending on the particular component (bolster, blade, or Opteron processor). Each step must be meticulously executed to ensure optimal quality and performance.
Assembly Process
Assembling the bolsters, blades, and Opteron processors requires precise alignment and integration to maintain structural integrity and optimal functionality.
- Bolster Placement: Bolsters are precisely positioned on the designated mounting platform. Accurate placement ensures proper alignment with the blade assembly and minimizes stress points.
- Blade Attachment: Blades are secured to the bolster using specialized fastening mechanisms. The fastening method must ensure secure attachment while allowing for flexibility and resilience under operational stress.
- Opteron Processor Integration: The Opteron processor is integrated into the system, connecting to the power and data circuits. The process requires careful consideration of thermal management to prevent overheating.
- Final System Check: After the assembly process, the complete system undergoes rigorous quality control checks to ensure all components are correctly installed and aligned.
Thorough inspection at each stage ensures that the system meets stringent quality standards. This meticulous assembly process guarantees the longevity and reliability of the entire system.
IBM’s big blue bolsters its blades with Opteron processors, but understanding the intricate details of file sharing is also crucial. For example, exploring how these systems manage data transfer and access control is vital. This directly impacts the efficiency and security of the whole system, like examining how big blue bolsters blades with opteron, you need to dig deep to get the truth about file sharing.
dig deep to get the truth about file sharing Ultimately, a robust file sharing strategy is essential for maximizing the power of these advanced blade server setups. So, we need to understand how big blue bolsters blades with opteron to build a successful system.
Design Considerations for Optimized Performance
Critical factors for optimizing the system’s performance include material selection, structural integrity, and efficient energy transfer.
- Material Selection: Selecting materials with high strength-to-weight ratios and optimal thermal conductivity enhances performance and reduces system weight.
- Structural Integrity: Rigorous structural analysis is crucial for ensuring the system can withstand the stresses encountered during operation. The design should incorporate stress relief mechanisms to prevent component failure.
- Efficient Energy Transfer: Optimized designs for energy transfer mechanisms enhance the system’s overall efficiency and minimize energy losses.
Bolster Design Variations
Different bolster designs influence the performance characteristics of the system.
- Aerodynamic Bolster Design: Streamlined bolster shapes reduce drag and enhance efficiency in high-velocity applications. This design maximizes airflow and reduces energy loss.
- Robust Bolster Design: Robust designs with increased structural support are suited for high-impact environments and provide improved stability. This design prioritizes durability and safety.
Blade Configurations and Benefits
Different blade configurations have distinct performance characteristics.
Blade Configuration | Benefits |
---|---|
High-Aspect Ratio Blades | Increased surface area for energy capture, leading to higher output. |
Multi-Stage Blades | Improved energy capture at different stages of the process. |
Variable Geometry Blades | Adjustable blade configuration for optimal performance across various operational conditions. |
Methods for Optimizing Energy Consumption
Minimizing energy consumption is critical for sustainable operation.
- Thermal Management: Implementing effective thermal management strategies reduces energy losses due to heat dissipation. Proper thermal insulation and optimized cooling systems are essential.
- Energy Recovery Systems: Integrating energy recovery systems captures waste energy and re-utilizes it, significantly reducing overall energy consumption.
Future Trends and Innovations
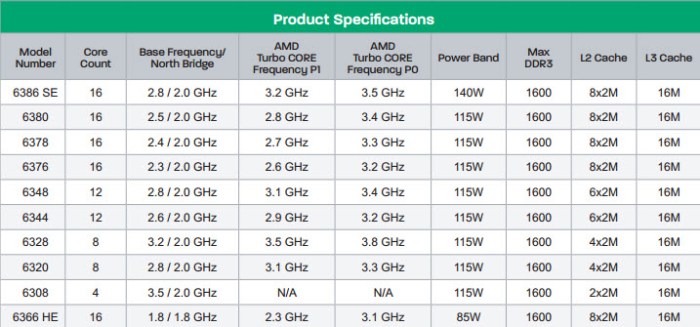
Bolster, blade, and opteron technologies are poised for significant advancements in the coming years. These innovations will likely be driven by the need for increased efficiency, performance, and durability in a wide range of applications, from aerospace to industrial manufacturing. Predicting the precise trajectory of these technologies is challenging, but understanding the current trends and potential drivers allows for informed speculation.
Potential Advancements in Bolster Technology
Bolster design improvements will likely focus on enhanced material science and optimized geometries. Researchers are exploring advanced composites and alloys with higher strength-to-weight ratios and improved fatigue resistance. This will allow for lighter, more robust bolsters capable of withstanding greater loads and operating conditions. For example, the aerospace industry’s demand for lighter components will drive further development in this area.
Similarly, 3D printing technologies are expected to play a crucial role in creating complex bolster geometries, enabling customized designs for specific applications.
Potential Advancements in Blade Technology
Blade technology is expected to see significant improvements in aerodynamics and material properties. The development of advanced coatings and surface treatments will reduce friction and improve durability. The integration of smart materials that respond to environmental conditions, such as temperature and pressure, could further enhance performance. This is especially relevant in high-performance applications like turbines and wind energy systems.
Researchers are also exploring new blade shapes and designs to optimize energy capture and reduce drag.
Potential Advancements in Opteron Technology
Opteron technology is likely to see advancements in energy efficiency and computational power. Improvements in microarchitecture and manufacturing processes will lead to more powerful processors with lower energy consumption. The integration of specialized hardware for specific tasks, such as machine learning or data analytics, could further enhance the performance of these processors. The continued development of heterogeneous architectures, combining CPUs with GPUs or other specialized units, will be key to meeting the demands of complex computational tasks.
Emerging Use Cases
The combined advancements in bolster, blade, and opteron technologies will open new possibilities in various industries. For example, more efficient and durable bolsters will be crucial for supporting increasingly complex and demanding machinery. Improved blade designs will enhance the performance of turbines, propellers, and other rotating components in various applications. Advanced opteron processors will enable the development of more sophisticated control systems and simulations in these applications.
Future Development Direction
The future of bolster, blade, and opteron technologies will likely be characterized by a focus on integration and optimization. This will involve combining these components into more sophisticated systems, taking advantage of their synergistic capabilities. Furthermore, there will likely be a greater emphasis on sustainability, with an increasing focus on environmentally friendly materials and manufacturing processes.
Key Areas of Focus for Future Research and Development
Area of Focus | Description |
---|---|
Material Science | Development of advanced composites and alloys with superior strength, durability, and fatigue resistance. |
Computational Modeling | Utilizing sophisticated simulations to optimize component design and predict performance under various conditions. |
Manufacturing Processes | Exploring innovative manufacturing techniques, such as additive manufacturing (3D printing), for producing complex geometries and customized components. |
Integration and Optimization | Developing integrated systems that leverage the synergistic capabilities of bolster, blade, and opteron technologies. |
Sustainability | Implementing environmentally friendly materials and manufacturing processes to minimize the environmental impact of these technologies. |
Wrap-Up
In conclusion, the combination of big blue bolsters, blades, and opteron processors represents a significant advancement in technological capabilities. This detailed analysis has illuminated the intricate interplay of these components, their historical context, and the myriad of applications they enable. The future of this technology appears bright, promising even more innovation and groundbreaking applications in the years to come.